Key Selection Criteria for Metal Binder Jetting Additive Manufacturing
By Ryan Martin |
09 Feb 2021 |
IN-6075
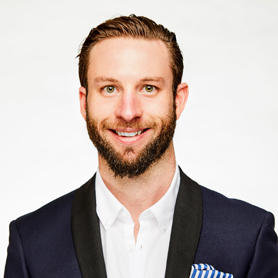
Log In to unlock this content.
You have x unlocks remaining.
This content falls outside of your subscription, but you may view up to five pieces of premium content outside of your subscription each month
You have x unlocks remaining.
By Ryan Martin |
09 Feb 2021 |
IN-6075
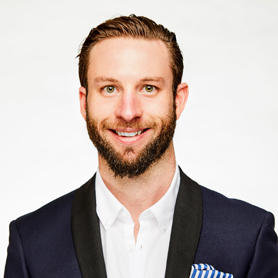
Metal Binder Jetting Moves Up the Maturity Curve |
NEWS |
Metal Binder Jetting (MBJ) is a tool-less manufacturing process that offers a number of benefits versus conventional manufacturing, including: 1) more complex designs, 2) assembly consolidation, 3) mass customization, 4) shorter lead times, 5) more flexible volumes, 6) localized manufacturing, and 7) digital inventory. The combination of these benefits with recent market advances is driving the MBJ landscape from prototypes and tooling to production and end use parts. This is a level of maturity that makes it important to understand the differences and key selection criteria to evaluate the various solutions already in the market and those coming soon.
Companies that have commercialized or announced their development of production focused MBJ technology include Desktop Metal, Digital Metal, ExOne, GE Additive, and HP. Of these, only Desktop Metal, Digital Metal, and ExOne have commercially available, production focused MBJ solutions today.
Market Composition |
IMPACT |
MBJ was originally conceived in 1993 at the Massachusetts Institute of Technology (MIT), before Extrude Hone obtained an exclusive license to commercialize the technology in 1996. ExOne, which was spun off from Extrude Hone in 2005, was the only company to offer an MBJ solution until the early 2010s, when the initial MIT patents for the technology began to expire. Its main attraction as a technology is that it is superior to alternatives, like powder bed fusion, in terms of speed, cost, and scalability.
All systems perform the same steps: 1) printing, 2) drying/curing, 3) depowdering, 4) sintering, and 5) powder recycling. Historically, most MBJ Original Equipment Manufacturers (OEMs) provided only the printer, relying on third parties for the other components (e.g., all use or have the option to use a third-party sintering furnace). Now, there are turnkey solutions and more integrated approaches wielding significantly higher throughput/speed that make MBJ a stronger candidate for higher production volumes.
Key Selection Criteria |
RECOMMENDATIONS |
The main difference in how companies approach each step of the binder jetting process is in the core technology, specifically in the printing step. Printing differs by speed, printhead technology, binder chemistry, safety (whether an inert environment is used), powder specifications, and material handling (e.g., powder deposition and spreading technology (i.e., powder recoating)). Another difference is the use of the same or comparable hardware across product families, allowing users to scale process more quickly. Desktop Metal employs this approach with the Production System P-1 and P-50 and ExOne does the same with its Pro series. As the market continues to evolve, the most important criteria to monitor can be segmented into five main categories:
- Process Capabilities: The first and most important criterion is whether the machine can produce the desired part geometry and material properties. Closely following and related are cost (i.e., can the desired geometry be produced at a competitive rate?) and volume (i.e., can the desired quantity of parts or products be produced?). For MBJ to be relevant to a particular application, all four characteristics—geometry, material properties, cost, and volume—must be achieved. Traditionally, MBJ is best suited for parts smaller than a basketball, though systems with larger build boxes (X1 160Pro) have recently hit the market. The other important aspects of process capabilities are quality and repeatability. Quality refers to resolution, surface finish, and material properties. Repeatability is the ability to produce uniform parts throughout a build and across multiple builds.
- Production Economics: At a high level, volume production economics in MBJ is a function of throughput (parts production during a given time period), hardware cost, and running cost (raw materials + consumables + labor + general operations). Including upfront hardware cost and associated depreciation is critical for assessing production economics and part costs, as omitting this element effectively removes productivity from the equation. Higher throughput systems benefit from the ability to depreciate upfront costs over a larger quantity of parts. This is important because while some systems may support a low running cost, they may lack the required part production capacity for a given application.
- Materials: MBJ users want 1) sufficient breadth of materials for different applications, 2) transparent and attainable material sourcing and pricing, and 3) strong material properties (hardness, yield strength, elongation, density). Standards are still being developed for binder jetting on the materials side, but many OEMs are qualifying materials to the Metal Powder Industries Federation’s (MPIF) 35 specifications. There are two schools of thought for material sourcing: 1) some OEMs have an open powder platform (Desktop Metal Production System P-1 and P-50, ExOne, HP Metal Jet) and 2) some have a closed powder platform (Digital Metal P2500, Desktop Metal Shop System). For more industrial manufacturers, the additional flexibility of an open powder platform is a big benefit as it allows customers to source the lowest cost option directly from MIM powder suppliers. The drawback to this approach is that customers may have to fine tune the print process more and create custom sintering profiles based on the powder vendor. Closed powder systems may result in higher raw materials costs, but often result in more plug-and-play offerings that provide greater accessibility to customers new to binder jetting without metallurgy or powder sourcing experience.
- Software: Software splits into 1) Computer-Aided Design (CAD), 2) build prep, and 3) process simulation. CAD software is always from a third party (SOLIDWORKS, Catia, NX, etc.). Most binder jetting systems use Materialise Magics as build prep for support generation, part nesting, and creating job files—part nesting is key for driving part economics (most parts get to 15% to 20% nesting density; increases in nesting density improves production efficiency and decreases part costs). Third-party build prep software is common but can be an expensive additional cost (US$10,000 to US$20,000+). For this reason, some companies include their own (e.g., Desktop Metal has Fabricate MFG), in addition to supporting third-party tools like Magics and NX. Process simulation is a more complex capability most often met by traditional software simulation companies (e.g., Siemens, MSC Software, Dassault Systèmes, Ansys, Autodesk, etc.), although Desktop Metal recently released its own software (Live Sinter) for sintering process simulation as well.
- Completeness of Solution: The degree of automation and whether each component is offered as an integrated solution, or from a third party varies by provider. For example, except for the Desktop Metal Shop System and ExOne InnoventPro (through a partnership with Rapidia), all offerings use or will use a third-party sintering furnace like those used in metal-injection molding (MIM). In theory, this enables MIM manufacturers to transition to additive manufacturing (AM) or more seamlessly incorporate it into their workflow. While users of these systems also have the option to leverage third-party solutions, it is typically easier to work with a single supplier with a tightly integrated offering.
The benefits of MBJ are manifold. For machine shops, MBJ eliminates tooling and job setup costs, and makes small and medium jobs economically viable. For OEMs, it provides an unprecedented level of flexibility and agility across geometries, volumes, and requirements. For the market, it introduces a new set of possibilities for innovation and design, at a competitive cost per part. But when evaluating how and where MBJ fits into your organization, there are really five key criteria to consider: 1) process capabilities: can it do the job; 2) production economics: can it produce a sufficient volume of parts at a cost competitive with current/conventional manufacturing methods; 3) materials: which materials are required and what is the level of comfort with metallurgy and material sourcing; 4) software: what is the workflow; and 5) completeness of the solution: is it turnkey. Taking these criteria into account will help structure and define a successful path forward.